Have you ever thought about how plastic bottles are made in a plastic bottles factory? Factories turn raw materials into bottles you use every day. They mainly use PET, LDPE, and HDPE. These materials are strong and can be recycled. Knowing about these materials and machines is important as it shows the environmental effects. Almost 600 billion bottles are used worldwide yearly. Making them uses up resources and creates waste. By learning how a plastic bottles factory works, you can see the good and bad of plastic bottles.
Key Takeaways
- Understanding the types of plastics used in bottle production, such as PET, LDPE, HDPE, and PC, helps you appreciate their unique properties and recycling potential.
- The manufacturing process of plastic bottles involves careful steps, including preparing raw materials, creating preforms, and using techniques like blow molding and injection molding.
- Quality control is crucial in ensuring that plastic bottles are safe and durable, with tests for strength, pressure, and chemical safety being standard practices.
- Recycling plays a significant role in reducing environmental impact; participating in recycling programs can help conserve resources and minimize waste.
- Being aware of the environmental concerns associated with plastic bottles encourages responsible usage and disposal, promoting greener practices.
- The flexibility and affordability of plastic bottles make them essential in the packaging industry, impacting consumer choices and market trends.
- Learning about the production process empowers you to make informed decisions about plastic use and supports the push for more sustainable practices.
Types of Plastics Used in Plastic Bottles Factory
In a factory, knowing the plastics used is important. Different plastics have special features. These features make them good for different uses. Here are the main plastics for making bottles:
PET (Polyethylene Terephthalate)
PET is common for drink bottles. It is clear, light, and strong. PET can be shaped into many forms. This makes it useful for different bottle designs. It keeps liquids safe because it is waterproof and resists chemicals. PET is fully recyclable. This means it can be made into new bottles. This recycling helps the environment.
LDPE/HDPE (Low-Density/High-Density Polyethylene)
LDPE and HDPE are both polyethylene types. They have different uses. LDPE is good for squeeze bottles like lotions. It is flexible but not as strong as HDPE. HDPE is used a lot for bottles. It is cheap and tough. It keeps moisture out. HDPE works with many products like acids. You see HDPE in milk and juice containers. Both LDPE and HDPE can be recycled. This makes them good for the environment.
PP (Polypropylene)
PP is another plastic for bottles. It is strong and clear. PP is good for making strong bottles. It is used where strength and clarity matter.
Knowing these plastics shows how complex bottle making is. Each plastic has its own benefits. This helps make bottle production efficient and eco-friendly.
Polycarbonate (PC) is a key material for making plastic bottles. PC is used in bottles that need to be strong and clear. It is very tough and see-through, perfect for reusable water bottles.
In factories, PC goes through a careful process. It can handle high heat, which helps in shaping. Factories pick PC for items that must last long without losing quality.
Here are some main features of Polycarbonate:
- High Impact Resistance: PC can take a lot of force without breaking. This makes it great for strong bottles.
- Transparency: PC is clear, so you can see what’s inside.
- Heat Resistance: PC can handle hot temperatures, good for hot-fill and cleaning.
PC has many good points, but it affects the environment. Unlike PET or HDPE, PC is not recycled as much. Knowing how PC bottles are made and recycled helps make better choices.
Learning about bottle materials shows how making bottles is complex. Each plastic, like PC, has a special job in making different bottles you use every day.
Overview of Making Plastic Bottles
In a factory, making bottles starts with raw materials. Knowing these steps shows how careful and exact the process is.
Getting Materials Ready
First, factories get the materials ready. They use PET, LDPE, HDPE, and PC. Each one is good for different bottles. PET is light and strong, great for clear bottles. PC is tough and handles heat, used in reusable bottles.
Factories get these as pellets. These pellets are dried to remove water. This is important because water can ruin the bottles. The dry pellets are melted into a smooth plastic, ready for the next step.
Making Preforms
Next, they make preforms. A preform is a small plastic piece that becomes a bottle. Factories use machines to mold these preforms. The melted plastic goes into a mold to shape it.
This step is key because good preforms mean good bottles. Factories check each preform for weight, thickness, and clarity. This makes sure the bottles are strong and last long.
Reheat and Blow Machine (RBM) Process in Plastic Bottles Factory
In factories, the RBM process shapes preforms into bottles. It has two steps: reheating and blowing. Knowing these helps you see how bottles are made.
Reheating Preforms
First, preforms are reheated. Machines heat them to a set temperature. This is just below melting, so they stay strong. Reheating is key for making bottles. It keeps the preform ready for shaping. Factories control heat to keep quality high. This makes sure bottles are strong.
Blowing into Bottle Shapes
Next, preforms are blown into bottles. They go into a mold for shape. Air is blown in to expand them. This turns preforms into bottles. The mold decides the bottle’s look. Factories use tech to make sure bottles are right. They must be useful and look good.
The RBM process shows how heat and air make bottles. Factories use this to make bottles for drinks and more.
Injection Molding Technique in Plastic Bottles Factory
In factories, injection molding is key for making bottles. It has two main parts: mold setup and injecting hot plastic. Knowing these helps you see how bottles are made with care.
Mold Design and Setup
First, engineers design and set up molds. Molds have special shapes for different bottles. They must be exact so all bottles look the same.
- Precision Engineering: Engineers use special tools to make molds with fine details. This makes sure bottles have the right shape.
- Material Selection: Molds must handle heat and pressure. Steel or aluminum is often used because they are strong.
- Setup Process: After designing, molds go into machines. They must be lined up right so plastic fills them well.
Good mold design is important. It makes production fast and reduces waste.
Injection of Molten Plastic
Next, hot plastic is put into molds. This has several steps:
- Melting the Plastic: Plastic pellets like PET are heated until they melt. This liquid plastic is ready to use.
- Injection Process: The hot plastic is pushed into molds with high pressure. This fills every part of the mold.
- Cooling and Solidification: The plastic cools and hardens, taking the mold’s shape. Cooling time is important for quality.
- Ejection: After cooling, the mold opens and the bottle comes out. It’s ready for more steps or packing.
This process is carefully controlled. Factories watch temperature and pressure to make sure bottles are good. This method makes many bottles that are all the same.
By learning about injection molding, you see how factories use tech to make bottles. This shows how important precision is in making the bottles you use.
Blow Molding Technique in Plastic Bottles Factory
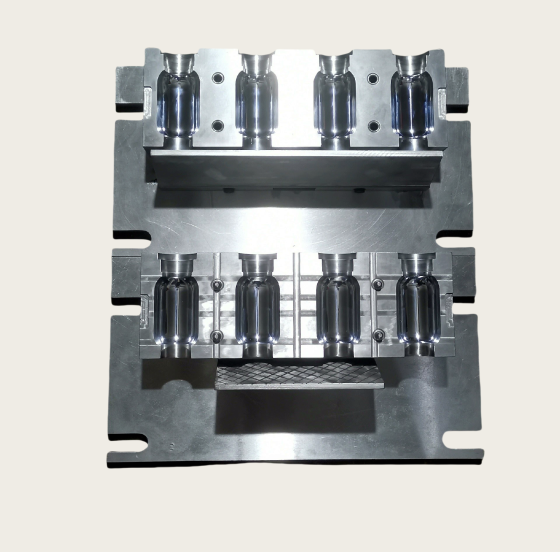
In factories, blow molding shapes bottles. It uses two main ways: extrusion blow molding and injection blow molding. Each way has its own benefits and uses. They help make strong bottles.
Extrusion Blow Molding
Extrusion blow molding is common for making bottles. First, plastic is melted into a tube called a parison. The parison goes into a mold. Air is blown in to shape it like the mold. This makes hollow bottles with even walls.
- Steps:
- Melt plastic into a parison.
- Put parison in a mold.
- Blow air to shape it.
- Cool and take out the bottle.
This method makes many bottles fast. It’s used for drink, soap, and other bottles.
Injection Blow Molding
Injection blow molding mixes injection and blow molding. It starts with making a preform in an injection mold. The preform moves to a blow mold. Air is blown in to shape it into a bottle. This way makes bottles with exact shapes.
- Features:
- Precision: Injection molds make detailed shapes.
- Material Saving: Less waste, saves money.
- Flexible: Good for small to medium bottles with tricky shapes.
This method is used for medicine, beauty, and food bottles. It makes bottles with neat tops and even walls.
Both methods show the smart tech in bottle factories. Knowing them helps you see how careful work makes strong bottles.
Quality Control and Testing in Plastic Bottles Factory
In a factory, making sure each bottle is good is key. Every bottle should be safe and strong. Quality checks help reach this goal. Let’s see how factories keep high standards with tests.
Checking Bottle Strength
Factories test bottles to make sure they are strong. These tests show if bottles can handle different things without breaking. Here are some tests:
- Drop Test: Drop bottles from a height to see if they break. This shows how bottles handle being moved or dropped.
- Pressure Test: Put pressure inside bottles to see if they burst. This checks if bottles can hold fizzy drinks.
- Impact Test: Hit bottles to see if they stay strong. This shows how bottles handle bumps or falls.
These tests make sure bottles are strong and last long. Strong bottles are good for many uses.
Testing for Safety Rules
Safety is very important in making bottles. Factories must follow rules to keep people safe. Here’s how they do it:
- Chemical Safety Tests: Check bottles for bad chemicals. This makes sure they don’t leak into drinks or food.
- Regulatory Checks: Follow rules from groups like the FDA. This makes sure bottles are safe to use.
- Labeling: Make sure each bottle has the right label. This helps find them if there are problems.
These tests make sure bottles are safe for people. Following rules also makes people trust the products.
Importance of Making Plastic Bottles in Factories
Effect on Packaging Industry
Making plastic bottles is very important for packaging. You see them everywhere, like in stores and at home. They are light and strong, perfect for holding many things. This makes them very useful for food, drinks, and personal care items.
- Flexibility: Plastic bottles can be shaped in many ways. This helps make special designs that look good and fit different needs.
- Affordable: Making plastic bottles costs less than using glass or metal. This helps companies keep prices low, which is good for everyone.
- Fast Production: Factories use new machines to make bottles quickly. They use methods like injection and blow molding to make sure bottles are made fast and well.
Plastic bottles do more than just hold things. They change how people shop and what they like. They also affect rules about the environment. Knowing this helps you see why making plastic bottles is important.
Environmental Concerns
Plastic bottles are helpful but can harm the earth. It’s important to think about how we use and throw them away.
- Recycling: Many bottles, like those made from PET, can be recycled. Recycling helps save resources and cut down on trash. Joining recycling programs helps the earth.
- Trash Problems: Throwing bottles away wrong can hurt nature. Factories and people need to handle trash better to stop this.
- Green Efforts: The bottle industry is trying to be more earth-friendly. They are looking for better materials and ways to make bottles. This includes using recycled stuff and making bottles that break down easily.
Research Findings: Checking bottles for quality is key. Watching closely helps keep bottles safe and good.
By knowing these earth issues, you can choose better ways to use and get rid of bottles. This helps the planet and supports the move to greener practices.
In a factory, making plastic bottles has important steps. First, get the raw materials ready. Next, make preforms. Then, shape them into bottles using special methods like injection and blow molding. New technology makes this process quicker and cheaper. Plastic bottles are important because they are light, strong, and useful in many ways. But, we must think about how they affect the earth. Finding better ways to make and use them can help reduce harm.
FAQ
What types of plastics are commonly used in plastic bottle manufacturing?
Factories mainly use PET, LDPE/HDPE, PP, and PC. Each plastic has special features. PET is strong and can be recycled. HDPE is tough and keeps out moisture.
How does the blow molding process work?
Blow molding has steps. First, make a preform or parison. Heat it and put it in a mold. Blow air inside to shape it. Cool it down and take it out. This makes strong, even bottles.
Why is quality control important in plastic bottle production?
Quality control checks if bottles are safe and strong. Factories do drop, pressure, and impact tests. They also check for bad chemicals and follow rules. This stops problems and keeps users safe.
How do manufacturers ensure the bottles are safe for use?
Manufacturers follow safety rules. They test for bad chemicals and follow FDA rules. Labels and checks make sure bottles are safe for food and drinks.
What role does recycling play in the plastic bottle industry?
Recycling helps the earth. Many bottles, like PET ones, can be recycled. This saves resources and cuts waste, helping the environment.
How do factories streamline the production process?
Factories make production fast with injection and blow molding. They use good machines to find and fix problems early. This saves time and keeps things running well.
What are the environmental concerns associated with plastic bottles?
Plastic bottles can hurt nature if not thrown away right. They cause pollution. Recycling and eco-friendly materials help reduce harm. People can help by recycling and choosing green options.
How do manufacturers cool the bottles during production?
Manufacturers cool bottles with cold water or liquid around molds. The way they do it can be different. Good cooling keeps bottles in shape and strong.
What is the significance of understanding the origin of materials in bottle production?
Knowing where materials come from is key. It keeps raw materials coming in, so production stays steady. This helps factories work better and keep quality high.
How does the use of preforms benefit the manufacturing process?
Preforms help blow molding by replacing parisons. They start the process evenly, cutting waste and boosting efficiency. This helps control the bottle’s shape and quality.